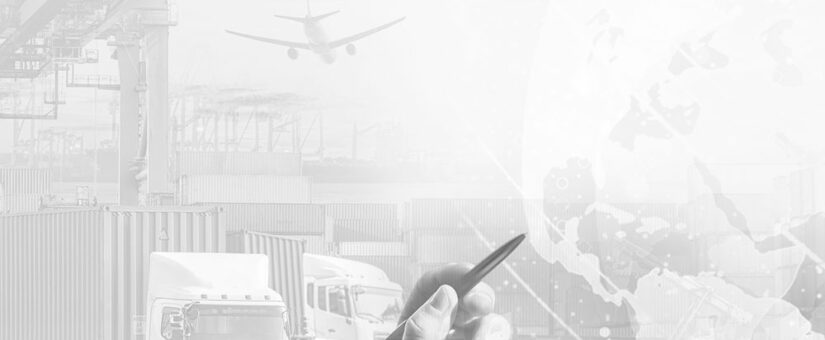
Leveraging Supply Chain Resilience Closer to Home
Leveraging supply chain resilience closer to home
Evaluating Mexico as a nearshoring destination
Conversations and projects with diverse clients in different industries across the globe are leading to a common conclusion: The old logic of exploring low-cost labor markets far from shore has reached a critical tipping point and is starting to lose its appeal as a cost-cutting option – apart from presenting numerous downsides. The range of benefits previously offered by offshoring is migrating closer to home, recently amplified by supply chain disruptions from the past years driven by the pandemic and a shifting global trade landscape.
Many markets and business leaders have set their sights on Mexico as an answer to their offshoring concerns – and as a key location for serving neighboring markets. Expecting to drive an increase of USD 35 billion in exports to the U.S.[1], Mexico’s government already aims to substitute at least 25% of North American imports from Asia with products made locally in the region[2].
While many businesses are ready to make this nearshore move to Mexico, uncertainty as to how and exactly where to start may pose a barrier to taking the next step.
This article aims to provide clarity by addressing some key questions that business executives should consider:
- Why are businesses paying attention to nearshoring now?
- What has turned Mexico into the number-one nearshoring location?
- Which factors do we need to weigh for choosing a site in Mexico?
[1] Estimates by the Inter-American Development Bank (IDB), June 2022.
[2] Statement by Mexico’s Foreign Minister Marcelo Ebrard after the North American Leaders’ Summit celebrated in Mexico (January 9-11, 2022).
Why are businesses paying attention to nearshoring now?
While not altogether new, nearshoring has gained additional prominence in view of the new reality facing global supply chains since 2020 marked by impacts ranging from rising labor and logistics costs to labor availability and overloaded shipping ports. Three broad factors have been driving this shift:
- Traditional offshoring sites are losing their competitiveness. After serving as an offshoring hub for decades, go-to destinations in Asia (mainly China) are becoming increasingly saturated, causing their benefits to erode. While rising labor costs have been the most relevant factor, growing concerns over intellectual property as well as deteriorating trade relations/conditions are accelerating this.
- Neighboring economies are maturing their foundations. New opportunities are clearly airing in countries closer to some of the globe’s largest local markets, especially the United States. While previously lagging in comparison, various businesses now believe that Mexico has made significant foundational strides by creating an attractive manufacturing landscape and skilled labor market.
- Businesses are eager to fortify their supply chains. Volatility bearing down on supply chains is also forcing business leaders to reassess their options. Increasing risk and uncertainty and transportation costs paired with ballooning transportation costs and decreasing service levels mean that conventional supply chain operations no longer cut it. Regionalization may be a way to achieve greater resilience while reducing risks and cost increases in transportation.
The concrete benefits of nearshoring
Supply chain considerations:
- reduce logistics costs
- shorten distances and lead times
- increase responsiveness and resilience
Positive impacts on the business:
- protect value
- maintain profitability
- significantly lower risk exposure
- boost agility when reacting to changing market conditions via close proximity
Why are businesses looking at Mexico as an attractive nearshoring location?
Maturing beyond serving merely as a low-cost location for manual operations, Mexico has transformed into a manufacturing powerhouse – with the sector receiving the bulk of foreign investment in the country. Nowadays, manufacturing sites in Mexico are serving global markets in a wide array of industries, including complex ones such as aerospace and medical devices.
Given the international context, Mexico has become one of the globe’s largest nearshoring markets, one that is particularly attractive for serving the US market. For example, the development of industrial real estate space increased in 2022 by 70% versus 2021, with a need to double this figure to support the needs of the companies that are expected to settle operations here in the following years. While efficiency was king in the past, driving the offshore movement, the factors businesses need to ensure stable operations, revenue and growth have changed.
Nearshoring: foundations beyond efficiency
Strong industrial capabilities developed in recent years, driving global competitiveness:
- 7-fold increase in R&D innovation centers in 10 years
- developed and diversified manufacturing sector (18% of GNP in 2021)
- 110,000 engineers graduate annually (20% of all graduates)
Logistics advantages to serve the North American market with shorter supply chains:
- lower transportation costs due to proximity to the U.S.
- lower tied-up capital (e.g. inventory)
- better service via lower time-to-market (g., <1 week vs 20-30 days from Asia) enabled by 54 border crossings to the US
- lower lead-times to source R&P materials, components, subassemblies, etc. being located between Asia and Europe
Structural and socioeconomic conditions that are particularly favorable:
- low/no duties via 14 free-trade agreements involving 50+ countries
- risk avoidance for intellectual property offered by robust regulations
- facilitated business planning and stability from steady inflation rates
- leverage for energy access and costs in a top energy region globally
Which factors do we need to weigh for choosing a site in Mexico?
Once your business has decided to move operations, a number of factors need to be considered when narrowing down options to the best-suited location. When helping companies identify sites at a regional or municipal level, we generally consider four key factors via an in-depth assessment:
- the labor profile
- start-up and operating costs
- the industrial and logistics environment
- government incentives
The relative weight of each factor will vary depending on the nature of your business as well as your strategy moving ahead. Doing a preliminary assessment based on the following quantitative and qualitative parameters can shed light on potential target regions within Mexico for executives considering nearshoring into the country.
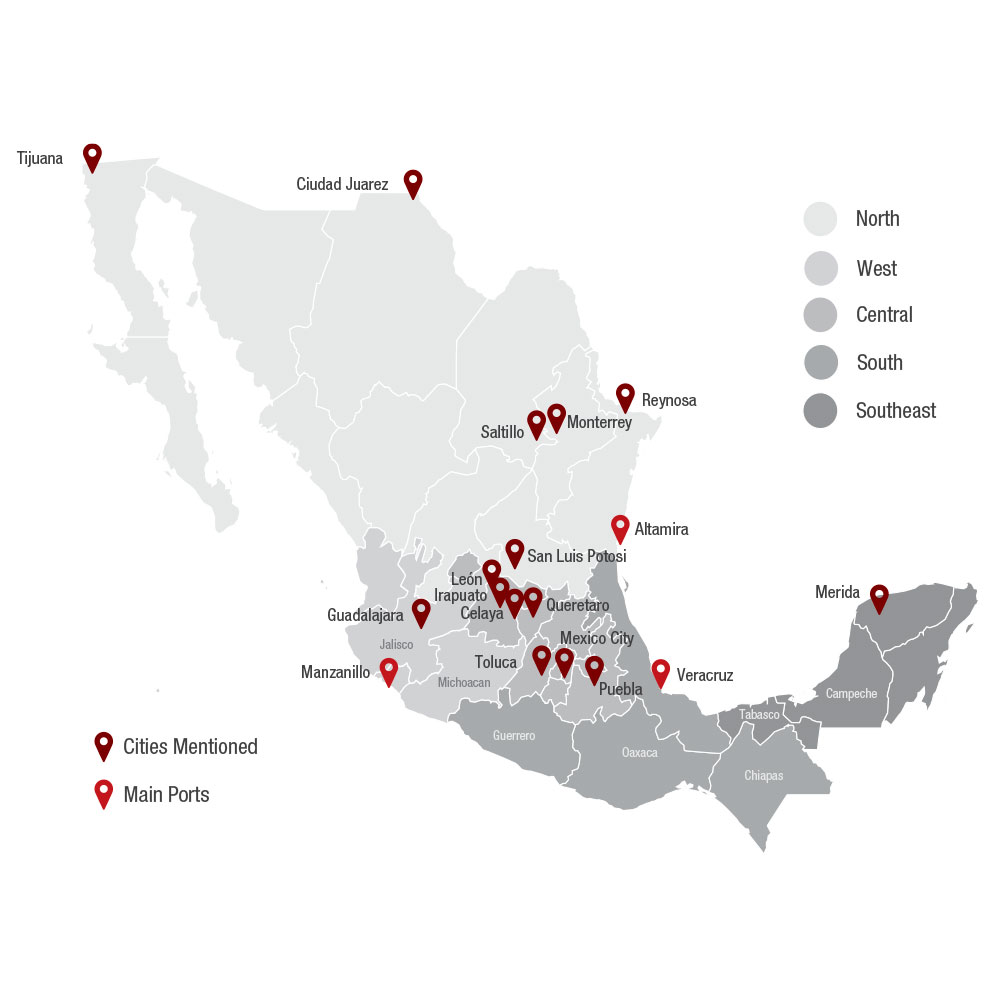
As the nature of each business will demand different workforce characteristics – from more manual-labor-intensive production lines to back-office support functions – labor is a key factor to be considered when assessing destinations that are more or less in line with what each company seeks in terms of talent. Having clarity of which are the labor requirements for the new operation, the assessment must consider a few related elements.
- The north, west and central regions of Mexico enjoy the highest degree of manufacturing sector development, with a much larger pool of skilled labor (88%) than the south and southeast regions – which have a historical economic development gap.
- The central region presents advantages over the north in terms of skilled labor, with more universities/tech schools per 100k inhabitants (8 versus 3) and people employed in manufacturing (40% versus 37%).
- Cities in the north region near or at the border such as Tijuana, Ciudad Juarez, Reynosa etc. have significant talent pools and has traditionally served as a key region for assembly operations (known as maquila) that leverage temporary import tax/duties benefits.
Labor Costs
- Average salaries for skilled labor in the north are 40% higher (USD 680/month) compared to the west and central regions (USD 480 USD/month) while salaries for unskilled labor are 42% higher in the north.
- Salary levels for professionals are generally aligned among major cities in the north, west and central regions, e.g. USD 2,150 – 2,600/month for a production engineer, with some cities in the central region being very competitive, e.g. USD 1,200 – 1300/month in Leon, Irapuato and Celaya.
- Most competitive wages are found in the south and southeast regions, though they lag behind in industrial and skilled labor development, apart for specific industries such as oil & gas in the states of Tabasco and Campeche.
Labor relations
- Mexico has a long tradition of union organizations, and 90% of production workers at companies with 25+ staff are unionized. The recently signed USMCA treaty includes tools to quickly enforce labor laws, help fight corrupt unions and improve working conditions to reduce the gap between the U.S and Canada.
- Labor relations are generally good throughout the country. There have been few labor strikes in the last four years (142 strikes within a universe of 5 million economic entities – a sign of good labor relations. Most of these strikes have been concentrated in the west region 48%, mainly in state of Jalisco – 39% of the total and 81% of the region, and the north region 35%, mainly in Tamaulipas, 27% of the total and 78% of the region.
Nearshoring your operations is not simply about placing factories or offices as close as possible to the border of the target market. Besides the fact that there may be multiple target markets such as the U.S. and Europe, the availability and cost of the inputs your operation relies on must also be taken into account. The following factors can provide a good preliminary estimation when developing a business case to set up operations.
Land and lease
- As expected, large cities present higher costs for land due to limited space, whereas smaller cities with more availability and expansion capacity of industrial parks present lower costs. This can drive significant land cost differences up to 5x-10x depending on the cities under evaluation, e.g. Mexico City at USD 183/m2 vs Reynosa – USD 36/m2. On average, the west region has higher costs for industrial real estate at USD 76/m2, followed by the central region at USD 70/m2. The southeast region is gaining momentum at USD 57/m2, with the development of cities such as Merida and the large potential development the trans-isthmus project will bring to the region.
- There is a deficit of available space versus expected demand due to local/foreign investment and the nearshoring trend. The cities in the Bajio subregion (central Mexico) have a better space availability (5.7% of total space) compared to the average across the north, central and west regions (4.8%), with the cities of Celaya, Irapuato and Leon offering particularly high availability (7.4%).
- Toluca, greater Mexico City, Monterrey and Guadalajara exhibit the highest land (USD 200/m2 average) and leasing (USD 5.30/m2 average) costs. Smaller cities in the north and central regions exhibit 30% – 70% lower costs on average.
Energy and water
- Energy costs vary across the country based on the regions and tariffs set by the national electricity authority, CFE. The energy demand intensiveness of the business can make these city/state differences a key factor for location decisions. As of 2021, cities in the north region had the most competitive energy costs, 10-16% lower than Mexico City and most cities in the central region.
- Cost variance for water is greater than for energy across sub-regions/cities, though the cost of water is much lower than energy and may be subsidized through official investment incentives in certain cases. The north region is 25-40% more competitive in water prices than the central and west regions.
Transportation
- The northeast states’ proximity to the border and location correlated to the “middle” of the U.S. makes them more competitive in terms of logistics costs, in general, than states in the central and west regions for serving the US market.
- Many plants located in Mexico serve other markets beyond the U.S. For operations established to serve additional markets, such as Europe, or those with a high dependence on imported raw materials e.g., from Asia, a location closer to Mexico’s major ports such as Manzanillo, Veracruz etc. is a smart choice – making cities in the central region the most attractive.
- The ideal location from a transportation perspective will depend on the relevance of imports/exports to other regions versus trade with the U.S. and the nature of the goods transported.
When assessing the location of a new operation, evaluating qualitative factors can be as important as financial considerations. Gaining clarity on qualitative matters such as how safe one location is compared to others, if companies in similar industries already exist there or how good the infrastructure in the area are highly relevant and can have a significant financial impact on the final decision.
Security
- Mexico is a relatively safe destination for manufacturing investments, despite bad press particularly associated with significant violence episodes in some border cities such as Ciudad Juarez.
- Large industrial cities in the northeast region such as Monterrey and Saltillo rank high across factors such as vehicle theft, homicides, kidnapping and crime – with rates being 35-75% lower than the national average.
- Some cities in the south region are considered some of the safest in the country, with Merida leading nationwide with the lowest figures in terms of vehicle theft, kidnapping and crime.
- The Bajio subregion has had a recent spate of crime mainly targeting strategic government operations mainly related to fuel transportation. Cities such as Leon, Celaya and Irapuato have high rates of homicide and crime, consequently scoring low on security perception by the population.
Industrial development
- The largest cities have traditionally been magnets for national and foreign industrial investment, having turning into industrial poles. This concentration in a few cities/regions has diminished over time and allowed other cities to industrialize, especially in the wake of NAFTA/USMCA and FTAs with other regions.
- The Bajio subregion has attracted a large share of investment, now surpassing many cities in the north – as reflected in industrial GDP per capita. Combined, the cities of Leon, Queretaro and San Luis Potosi now have more industrial plants with over 100 employees than Monterrey, a traditionally industrial city.
- The northeast region has 20-60% more installed energy capacity than the central and west regions, with future availability being a challenge as several investment projects have lagged behind.
Logistics infrastructure
- Federal and local governments have invested in developing logistics infrastructure to support Industrial development and growth, with states like Queretaro in the Bajio subregion successfully sustaining, planning and developing projects to attract investment.
- The main industrial cities have good access to major highways, with support from the government and foreign investment. Cities along the major highway corridor from Mexico City to the Texas border have a competitive advantage for goods transport to the U.S.
- Greater Mexico City and the central region cities benefit from good access to ports in the Pacific, e.g. Manzanillo, and the Gulf, e.g. Veracruz and Altamira.
Sustainability
- Despite recent regressions, Mexico has progressed in its environmental policies, though specific conditions must be considered depending on the type of industry and processes.
- Water availability and conservation is becoming a challenge nationwide due to climate change and overexploitation. Expected access to renewable water is low in central and northeast Mexico, with the Bajio subregion generally scoring the lowest overall. Guadalajara, Puebla and San Luis Potosi have made significant efforts to improve water utilization and renewal.
- The northeast and central regions present similar mid-to-mid-high scores in terms of wastewater treatment, with outliers such as Greater Mexico City having very low scores given significant topographical constraints that limit capitalizing the available opportunities.
- Reforms to energy laws and campaigns to promote foreign investment have led to advances in alternative energy sources. The south and southeast regions have the most installed capacity of renewable energy (Veracruz, Oaxaca and Campeche states). The Bajio subregion cities have a mid-range score in terms of availability, with the northeast region and Greater Mexico City trailing behind by far.
Finally, incentives can have a huge impact on decisions to select a certain destination for setting up a new operation. It’s not uncommon for governments at the national, state or city level to grant benefits packages to attract investments. These can be as large as multi-year tax exemptions or specific incentives such as land grants, infrastructure investments (e.g. roads), services grants (e.g. water) and more. When making an overall calculation for a nearshoring business case, it’s critical to consider such potential incentives as an integral part of the location assessment.
- States and city authorities are keen to offer incentives to attract investments, making it advisable to start conversations with these early on when evaluating potential locations.
- The current federal administration is placing particular focus on the development of the south and southeast regions of Mexico, specifically the area where the trans-isthmus corridor is being developed – an interoceanic alternative to the Panama Canal aimed at reducing international freight transit times. Incentives being granted by the federal government include a full income tax full exemption for five years followed by a 50% exemption for the subsequent three years, property tax exemptions, VAT exemptions (for trade between companies located in the corridor) and more.
What key success factors should we consider when taking the first steps?
As nearshoring represents a strategic move for the business, several key considerations should go into an assessment of potential locations in Mexico – or any other nearshoring destination.
- Being a business decision, different areas in the company need to be involved throughout the evaluation and decision-making process. Not only will this ensure an integrated overview of the different location options and a selection that is really best-suited to the operation, it will also drive buy-in among the areas and key stakeholders involved. Professionals focused on supply chain (planning, manufacturing, engineering, production, HSE etc.), finance, marketing, legal, HR and more should be made part of a multifunctional team directly participating in the evaluation with a steering committee of key stakeholders creating for decision-making.
- Before diving into the assessment factors, it’s important to arrive at a high-level definition of which regions in Mexico offer a better fit for the nature of the business, the market(s) or region(s) to be served and which countries materials, components and sub-assemblies will be sourced from. This will enable the leadership to narrow down the list of potential target locations and allow a more focused evaluation from the multifunctional team.
- Take a pragmatic approach when considering the factors in the evaluation. These should be structured in a simple scorecard, with metrics considered for each one defined. It’s important to assess the availability of data for each metric and element, as some can imply a significant research effort, the definition of assumptions and extrapolations. Ensuring the right balance between being comprehensive and the effort required is key. Fortunately, large amounts of public data is available about Mexico in both government and private institutions (all of the metrics described above have been used by Integration in location assessment projects). Once metrics have been defined, the multifunctional team can set score weights for each overall factor and its metrics. This will help ensure alignment on the factors and metrics that are most relevant for the evaluation – as these can differ from one company to another.
With this foundational analysis in place, the potential options can be short-listed to 2-3 locations that should undergo an on-site assessment. This stage is important as it will allow for further quantitative and qualitative details based on interviews and visits to industrial parks, government authorities, chambers of commerce, peer companies, universities etc. With this full picture in place, your business will be in an advantageous position to decide where to locate in Mexico and start reaping the benefits of operations closer to shore.
TALK TO US
- On 24 February 2023